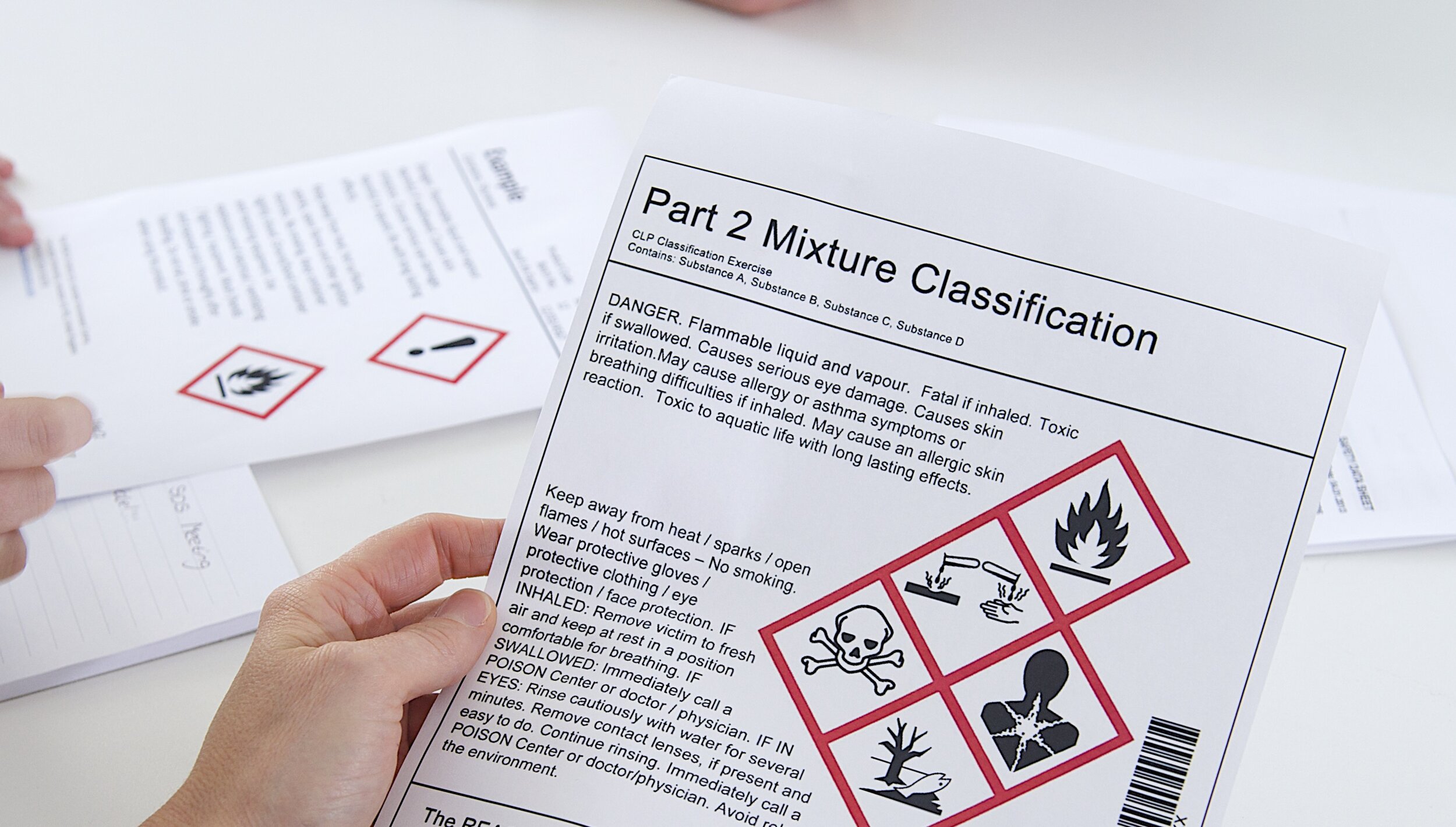
The use of automation in Safety Data Sheet authoring
Introduction
Generating a compliant SDS is a critical process for any organisation placing chemical products on the market. With a myriad of regulatory data and stakeholders involved in the process, managing the creation of an SDS can be an incredibly complex task.
Authoring systems and integrated content solutions have emerged to facilitate the generation of SDS, but the full benefits can only be realised when such systems are integrated hand in-hand with best practices for SDS generation. In this whitepaper we will explore the benefits and shortfalls of the different types of SDS authoring systems.
Safety Data Sheets (SDS) are widely accepted and legally mandated documents that inform users of the hazards of substances or mixtures and provide advice on safety precautions and risk management measures. The Globally Harmonised System (GHS) of Classification and Labelling attempts to harmonise the format and content of SDS into 16 sections and specify a minimum amount of information required.
Despite widespread implementation of GHS, country-to-country variation remains. Variation impacting on the classification, product labelling and information contained within the SDS, may be due to the requirement to maintain an equivalent level of protection when transferring from earlier chemical safe use policies to GHS, or current country or region-specific requirements. These local requirements may include mandatory or minimum classifications, occupational exposure limits, waste disposal methods or other relevant legislation.
When a company places a product on a market that has implemented GHS, it generally needs to identify and classify any hazards associated with the substances contained in that product, and produce a compliant SDS and label specific to that country or region. Together with the variations outlined above, and considering that GHS is constantly evolving, the changing regulatory landscape poses challenges for companies and SDS authors who wish to ensure that their SDS and labels are kept up-to-date.
This whitepaper shares Yordas Group’s experience and opinions of working with fully automated, manual and semi-automated authoring systems to deliver SDS and labelling to global markets, and to manage and accommodate the subtleties or specificities of regional or country-to-country GHS variation.